Product Test
Made to last.
Product: Concrete
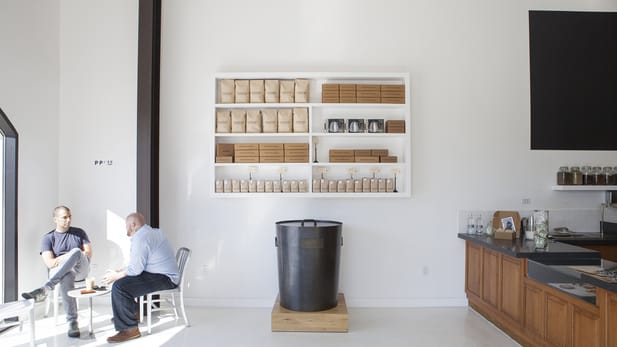
Floor Preparation
Floor Overlay
Product: Concrete
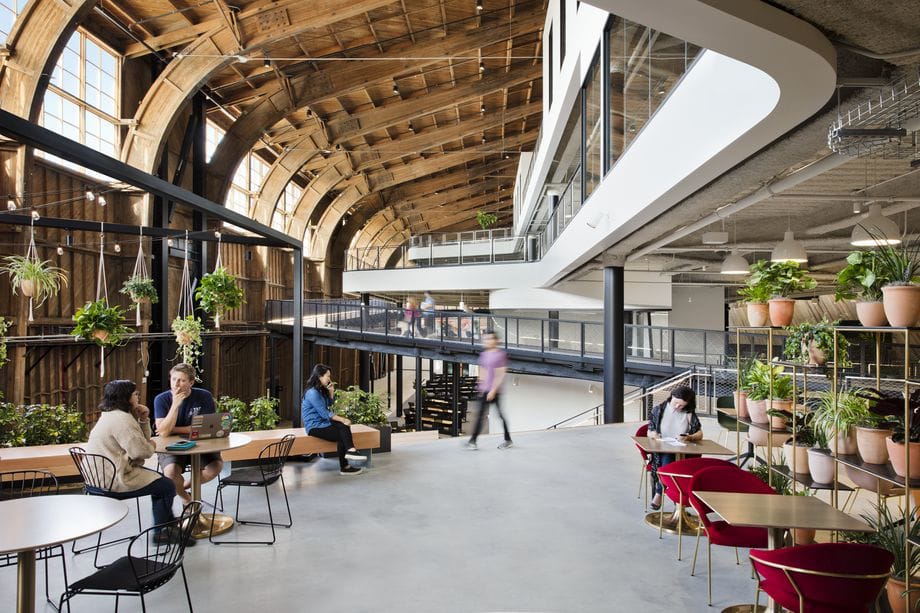
Floor Polish
Epoxy Coating
Epoxy coatings are ideal for floors that require protection from or may come in contact with oils, harmful acids or chemicals. Concrete is a very durable material, however, it is not resistant to most chemicals used in commercial or industrial settings without some type of coating.
An epoxy floor sealer is design to protect concrete floors or other floor systems from water, dust, moisture, and chemical resistance. You’ll find an application like this used on commercial production floors, warehouses, mechanic shop floors, showroom areas and garage floors. Sealants also help concrete stand up to abrasion, scuffing and is ideal for high traffic areas. Sealants are also used to cure new concrete floors.
Epoxy coatings & Sealants system are used for:
- Warehouses
- Industrial Floors
- Production Floors
- Food Service Industry
- Cafeterias
- Hospitals
- Showrooms
- Auto Mechanic Bays
- Food Services Industry
- Schools
- Retail Stores
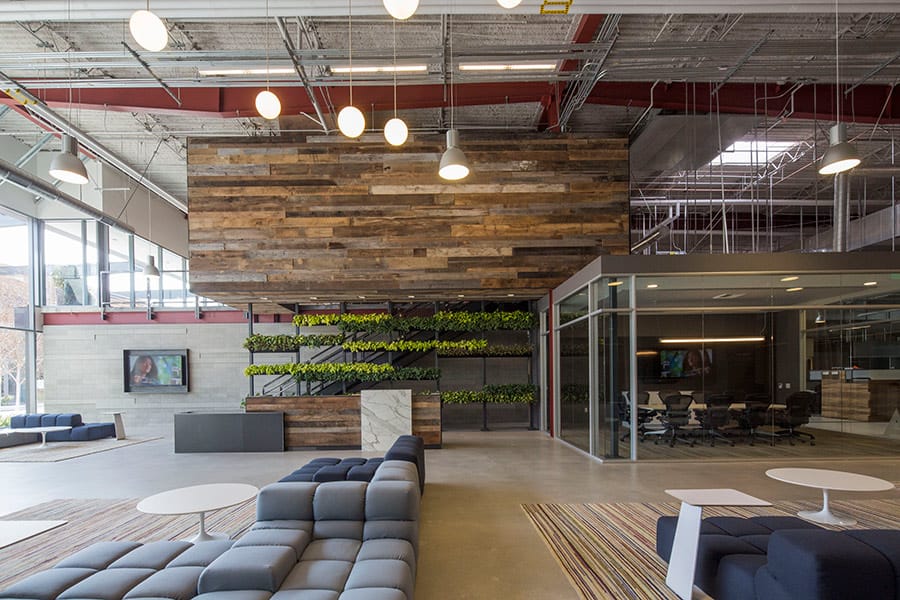
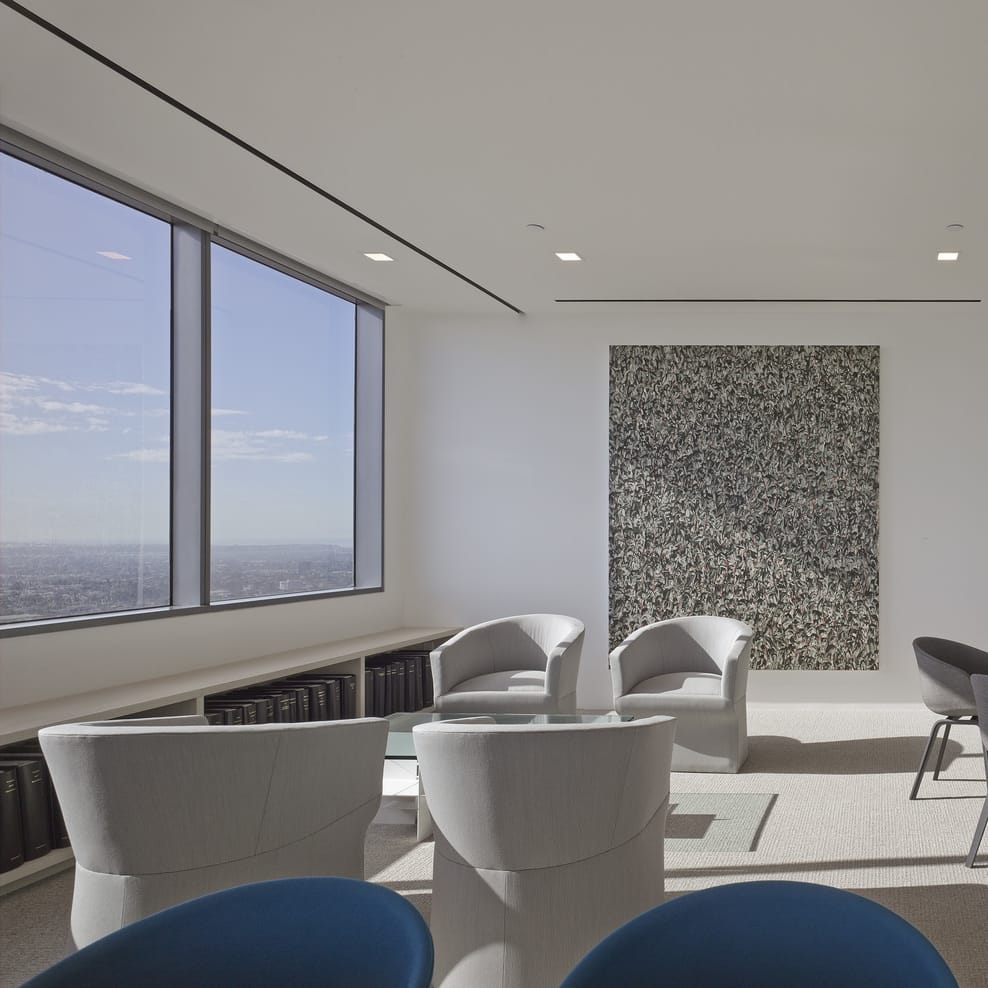
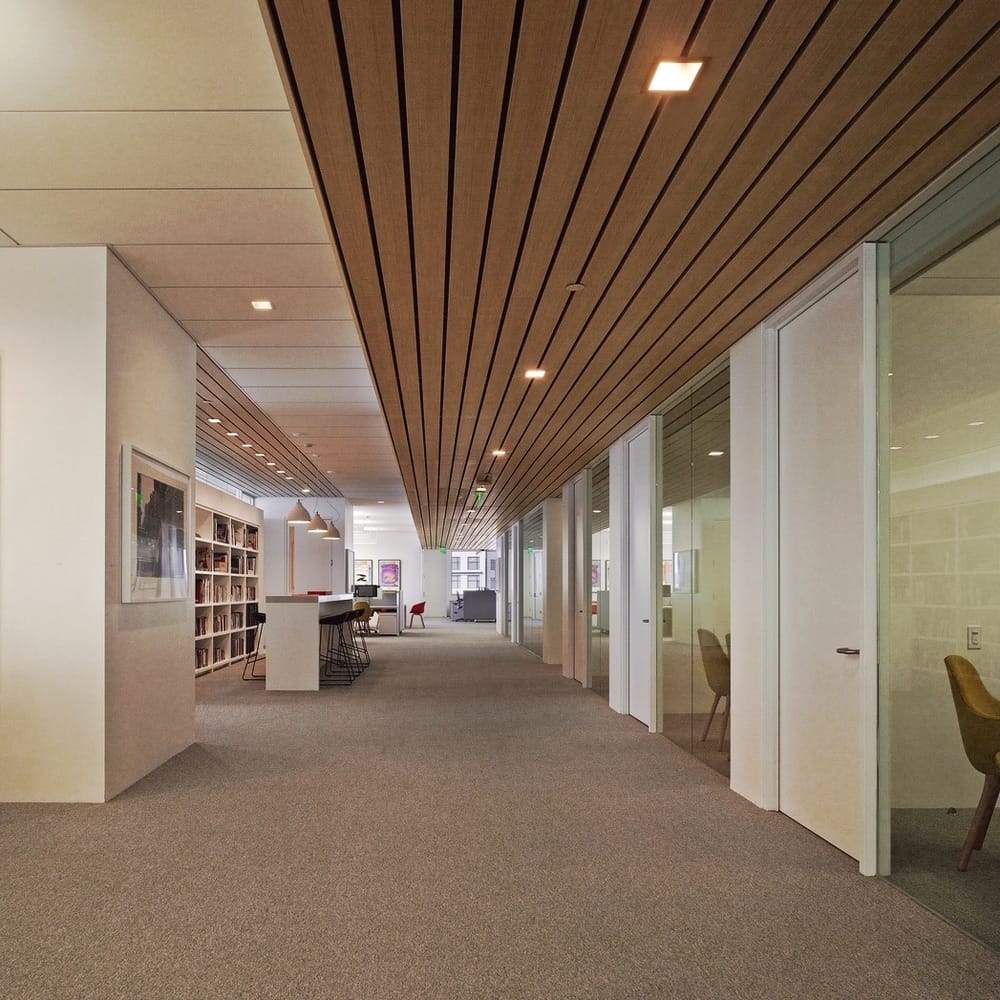
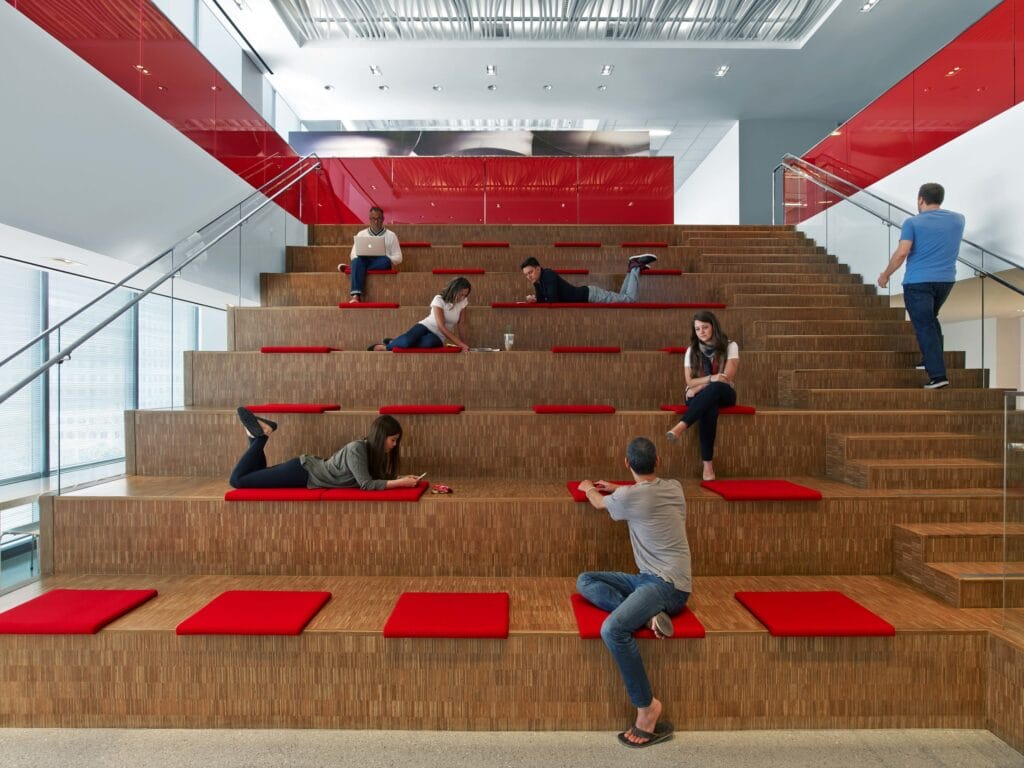
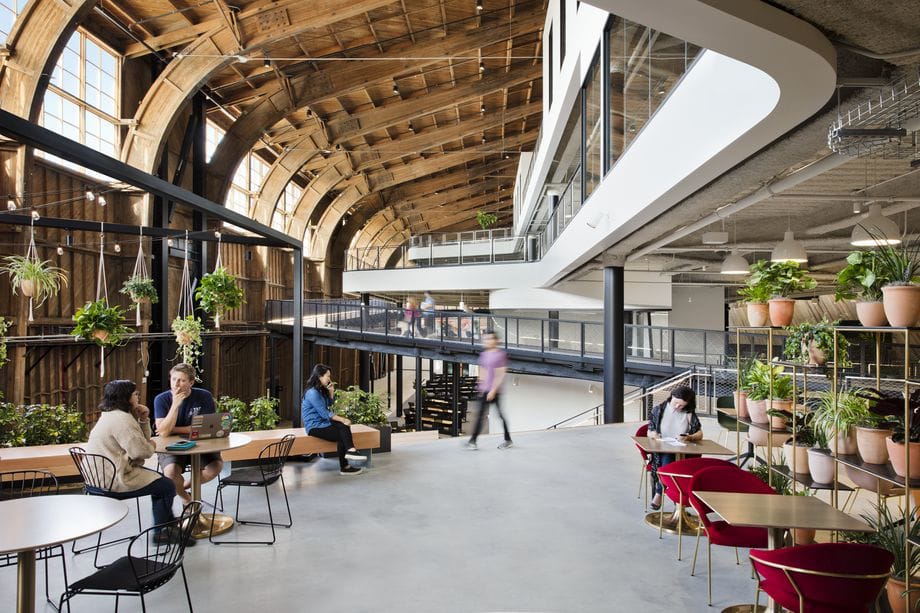